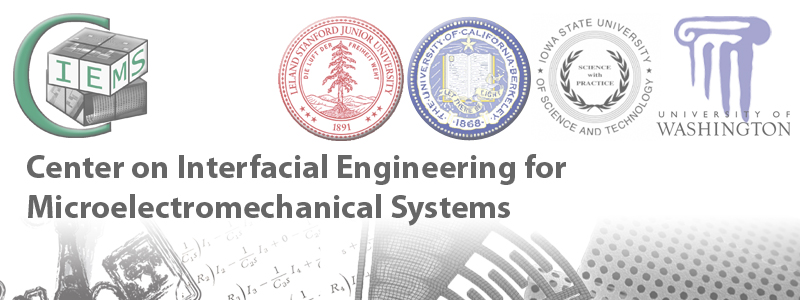
Faculty
Roger HoweOlav Solgaard
Fritz Prinz
Roya Maboudian
Krishna Rajan
Karl Böhringer;
Babak Parviz
Sponsors
AgilentAnalog Devices
Boeing
Bosch
Cambridge NanoTech
Honeywell
Intel
Microsoft
Samsung
Syngenta
DARPA MTO
Links
CIEMS Graphics
Presentations
Presentations
Errors, omissions, corrections? Email:
Research
The Center on Interfacial Engineering in Microelectromechanical Systems (CIEMS) is advancing the surface-science and engineering of microstructural materials, coatings, and processes to enhance the capabilities and performance of micro and nanoelectromechanical systems, through funding interdisciplinary, collaborative research projects at Stanford University, the University of California at Berkeley, the University of Washington and Iowa State University.Motivation
A well-known outcome of scaling into the micro and nanometer dimensions is the dominance of surface over bulk phenomena in determining electronic, mechanical, and electromechanical behavior. The existing knowledge base is on surface phenomena is concentrated on narrow material combinations in specific packaging environments. The incomplete knowledge about MEMS surfaces and their role in determining fracture and fatigue mechanisms has resulted in designers adopting “rules of thumb” which ensure large safety margins. Such conservative designs result in lower sensitivities for devices that depend on the absolute amplitude of motion, such as vibratory rate gyroscopes, and limit the range of microactuators in applications such as micro-optical scanners. The expansion of MEMS into new applications, especially those involving contact or exposure to harsh environments, has been hamstrung by the lack of basic understanding of structural surfaces, surface coatings, and microencapsulation processes and how they impact the performance of MEMS.Microshell Test Environment
Central to the research strategy of CIEMS is to utilize recent progress in sealed microcavity encapsulation to establish a benchmark, reproducible microenvironment for characterizing surface and interface properties. Prof. T. Kenny and his group at Stanford, together with Bosch RTC have recently demonstrated such a sealed microcavity process. After patterning the structural layer, an additional layer of SiO2 sacrificial material is deposited and then the first layer of the polysilicon encapsulation. After patterning etch-access holes, the microstructure is released by vapor-HF etching and then fully sealed by deposition of conformal LTO or polysilicon.The microcavity process has several advantageous features for creating a standard microenvironment for evaluating surface properties. The device is sealed in an ultrapure environment at high temperature with hydrogen as a residual gas and never exposed to external environments after the encapsulation is complete. After sealing, wafers or individual devices can be heated to 500C or higher, while maintaining the ultrapure environment.
Additionally, the vacuum cavity is a functional device component. Vacuum provides thermal, yet sufficient electrical continuity for thermonic energy converters and bolometers. Additionally, with an optically transparent cap, light could be coupled into a packaged photonic crystal.
Self-Assembly
Self-assembly is an increasingly powerful tool for heterogeneous batch manufacturing of microsystems. It allows for the assembly of micro parts onto unconventional substrates. To accomplish this, modeling and controlling the interfaces between components is being studied. The potential applications include thermo-electric coolers and multi-sensor platform on a contact lens.Photonic Meta Materials
The major barrier to deployment of optical MEMS is the presence of defects. Defects limit practical repeatability, accuracy and long-term stability of photonic crystals and optical metamaterials. New surfaces, treatments and design will be investigated to reduce the effect of defects on the optical characteristics of photonic crystals.Additionally, CIEMS will investigate a new approach to wafer-level, encapsulated optical MEMS based on the creation of photonic meta-materials. These materials are patterned on sub-wavelength length scales, to achieve the high reflectivity and filter characteristics that traditionally can only be achieved with metals and dielectric stacks. Unlike traditional metal-coated optical MEMS, such meta-materials can withstand the microshell encapsulation process.
Interfacial Contact
CIEMs will investigate interfacial nano-engineering for SiC based N/MEMS. At the present time, the performance of SiC devices is most often limited by the quality and stability of the ohmic contacts. Nickel based ohmic contacts produce roughening of the contact surface and excess C segregation upon annealing. To improve the contact, nanocrystalline graphitic carbon is being investigated. Additionally, Ion bombardment is being explored to improve corrosion resistance. Finally, CIEMS will use new thermally actuated test structures to test contact reliability.CIEMS will use Atom Probe Tomography to study interfaces to improve N/MEMS. CIEMS will compare modeling to experimental images to characterize surface degradation. Also, the imaging will allow the study of alloy contact interfaces to improve interfacial chemistry.